OSHA Compliance Resources
These resources provide a quick summary of important OSHA Regulations that printing operations need to meet. PRINTING United Alliance’s Government Affairs staff can help you with your OSHA compliance requirements, including, but not limited to, the topics below.
Control of Hazardous Energy Sources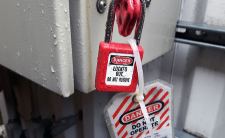
The OSHA standard for The Control of Hazardous Energy — or Lockout/Tagout (LOTO) works in conjunction with the machine guarding standard and serves to protect employees from injuries during servicing and maintenance of equipment. The regulation requires a formal written program, machine specific procedures, lockout devices, employee training, and an annual review of procedures.
CSB Reporting Rule
The Chemical Safety Board and Hazard Investigation Board (CSB) issued a new accidental chemical release reporting rule on March 23, 2020. This rule applies to all printing operations and is in addition to other reporting rules currently in place.
Electrical Safety
It is important to ensure all employees are aware of and regularly practice electrical safety. OSHA enforces specific requirements on handling and maintaining items such as breaker boxes, extension and flexible cords, pendant drops, power strips, etc. Familiarize yourself and your fellow workers with these electrical best practices.
Emergency Evacuation
OSHA’s Emergency Action Plan standard requires a company to develop emergency action plans for employee protection during times of emergencies such as evacuating the facility in the event of a fire. Printing operations with more than 10 employees are required to their plan formally written. Do you have all the required components in your emergency action plan?
Fire Safety
There are many topics encompassed by the term “fire safety”. A company must be equipped with a Fire Prevention Plan, the proper type of fire extinguishers, training on using fire extinguishers, operational emergency exits, and must properly manage and store flammable materials.
First Aid
Employers must comply with OSHA’s first aid standards. This includes having a formal first aid response plan, a first aid kit stocked with at least the minimum requirement items, and training employees for first aid response. Not only should employers evaluate their first aid response programs based on OSHA compliance requirements, but the specific needs of their workplace as well.
Hazard Communication Standard
All printing companies that use inks, toners, cleaning solvents, coatings, adhesives and other chemicals must comply with OSHA’s Hazard Communication Standard. The regulation requires the preparation of a written program, chemical inventory, Safety Data Sheets, labeled containers,
and to provide employee training on safe chemical use.
Hearing Conservation Program
OSHA's Hearing Conservation Standard requires employers to ensure that employees are not exposed to levels of noise in the workplace that can damage their hearing. If the levels in your facility are above the standard of the level of 85dB(A) on an 8-hour time weighted average exposure, you are required to implement a hearing conservation program. Perform a noise measuring test to find out if you are exempt from this requirement!
Machine Guarding
Safeguards or machine guards are physical barriers or equivalent devices such as light curtains that are designed to prevent equipment operators from accidentally contacting dangerous machine parts or areas that could result in an injury. All hazard areas are required to be guarded and there is no “grandfathering” of old equipment. This means that even if a guard was not originally installed on a piece of equipment, it is the responsibility of the printing operation to fabricate and install a guard. Be aware of the common hazards in the screen and digital printing processes so you can prevent accidents from occurring in your facility.
Personal Protective Equipment
OSHA requires all employers, regardless of size of facility, to conduct a formal written workplace hazard assessment to determine the type of personal protective equipment required to protect employees from injuries. Employers are required to provide this PPE as well as training on how to use it properly.
Powered Industrial Trucks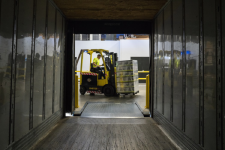
OSHA's standard requires employers to develop and implement a training program for all operators of powered pallet jacks and forklifts on safe operation including a formal practical evaluation. Make sure your program is meeting all the required components.
Recordkeeping and Injury Reporting Rule
OSHA has revised its requirements for recording and reporting occupational injuries and illnesses. All fatalities must be reported to OSHA within 8 hours and certain injuries and amputations need to be reported within 24 hours. Every March 2, companies with more than 20 full time, part time, or temporary workers need to electronically report their injury and illness data to OSHA.
EHS Consulting
Whether you are looking for information on how to avoid OSHA violations or how to develop a lockout/tagout program, PRINTING United Alliance can help.
Our resources provide an excellent foundation and the Government Affairs staff is available to answer your questions. If you need more in-depth assistance, our EHS Consultants are available for in-person facility visits to assist with any environmental, safety, and health problems you may be facing or want more information about.